Safely Shipping Flexible Metal Components
By: Hose Master | On: October 17, 2019

Hose Geometry and Flexibility
When it comes to flexible metal hoses and expansion joints, one factor that should not be overlooked is how to protect them during shipping. However, this is not always the first thought that comes to mind. After all, they’re made out of metal and are often selected for the ruggedness, durability, and flexibility that they provide a rigid piping system in critical and extreme applications. However, in order to maintain their flexibility in harsh conditions it is imperative that the hose or expansion joint’s geometry be maintained. The geometry refers to the design and shape of the hose or expansion joint, particularly the corrugations. It is the corrugations (also called “convolutions” when referring to expansion joints) that change their shape as movements are encountered and provide the hose or expansion joint’s desired ability to flex. These corrugations are carefully designed and formed in order to provide the longest-lasting product with the highest cycle life. Therefore, safely shipping flexible metal components is of vital importance to ensure the product achieves its desired function and longevity.
Protecting Metal Hose

The hose pictured above has experienced impact damage prior to installation. While the damage appears minor, it can be detrimental to the hose’s performance.
Special care should be taken to protect metal hose during shipping and before installation. If a corrugation on a hose becomes damaged, then the profile of the corrugation is changed. This means that it cannot flex as it was originally designed to and the performance of that corrugation is now compromised. Now, as bending stresses are applied to the damaged corrugation, the bending stresses cannot be properly deflected and are concentrated to where the metal has been creased by the dent. This concentration point is called a “stress riser” and the metal will fatigue most quickly at this point.
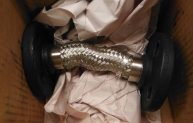
Stacking a hose on its flanges during shipment can compress the hose, loosen the braid, and lead to squirm in an assembly.
For corrugated metal hose assemblies, an outer braid layer provides a measure of protection to the underlying corrugations, but sometimes additional protection is needed depending on the assembly type. When shipping flanged assemblies, it is possible for the hoses to shift or move in the shipping container, causing damage as they bump into adjacent hoses. Shipping these assemblies vertically may prevent them from rolling around, but the weight of the flanges can compress the hose during shipping and cause the braid to become loosened. This loosened braid applies excessive stress to the corrugations when the hose is installed and pressurized. Once in service, the corrugations experience a burst of movement as they re-extend until the braid tightens back over the hose, causing the profile to deform. This fatal phenomenon is often referred to as “squirm.”
To avoid both “stress risers” and “squirm,” assemblies must be packaged carefully to avoid damage during shipping.
Protecting Expansion Joints

Shipping bars (painted yellow) help protect an expansion joint from movement during shipping.
Metal expansion joints present different concerns in regards to shipping. Any movement of the convolutions during shipping can damage the bellows or dramatically reduce cycle life. To ensure an expansion joint maintains its desired cycle life, hardware (such as the addition of shipping bars) is usually required to protect the unit during shipment and to prevent any movement of the bellows. After the expansion joint is installed, these shipping bars must be removed in order for the bellows to deflect properly.
Because expansion joints are offered in larger diameters than hoses, isolating the bellows from movements and protecting the unit from shipping damage can be challenging. To assist in this concern, EJMA (Expansion Joint Manufacturer’s Association) publishes a guide on properly handling and installing metal expansion joints that can be useful to installers.
Safely Shipping Your Flexible Metal Components
Being aware of problems that can arise when shipping flexible metal components can help to avoid potential damage and ensure the longest working life of an assembly. Once the hoses or expansion joints are received, additional care must also be taken when unpacking, handling, and installing them to prevent damage. For more information on proper shipping, handling and installing flexible metal components, please see our Metal Hose Operations & Handling Manual available on Hose Master’s website and included with every expansion joint we ship. If you have additional questions please feel free to contact us and we would be happy to help.
Copyright 2019, Hose Master, LLC
All Rights Reserved